Nell’era della digitalizzazione industriale, le aziende manifatturiero stanno rapidamente adottando nuove tecnologie per rimanere competitive. Genesis Group sostiene l’ integrazione di automazione avanzata, supporto remoto, interconnessioni tecnologiche e soluzioni personalizzate per le smart factory che rappresenta una trasformazione profonda nel settore. Questi sviluppi non solo migliorano l’efficienza e riducono i costi, ma aprono anche nuove possibilità per l’innovazione e la sostenibilità nella produzione.
Le soluzioni Smart Factory e le interconnessioni tecnologiche stanno trasformando il settore manifatturiero
1. Automazione dei Processi Produttivi
L’automazione dei processi produttivi è fondamentale per ottimizzare l’efficienza e aumentare la qualità del prodotto finale. Implementando sistemi robotici avanzati e algoritmi intelligenti, le aziende possono automatizzare compiti complessi e ripetitivi. Questo non solo velocizza la produzione, ma minimizza anche gli errori umani, migliorando la coerenza e la qualità dei prodotti. La capacità di monitorare e controllare in tempo reale ogni aspetto della produzione permette inoltre un intervento rapido in caso di anomalie, garantendo un flusso di lavoro ininterrotto e sicuro.
2. Smart Manufacturing e le tecnologie abilitanti a esso connesse
Per raggiungere nuovi standard in termini di flessibilità, rapidità ed efficienza, il mondo dell’automazione industriale è trainato da uno dei principali motori di trasformazione degli ultimi anni: lo Smart Manufacturing e le tecnologie abilitanti a esso connesse.
Nel 2024 sono riconfermati gli incentivi fiscali per la conversione a Smart Factory dal Piano Nazione Transazione 5.0. Il momento per adottare le tecnologie per l’automazione industriale 4.0 è quindi maturo!
La prima, e forse più importante, caratteristica della Smart Factory consiste in un elevato livello di connessione tra le varie parti dell’impianto. Queste tecnologie consentono una sincronizzazione perfetta tra macchine e sistemi informativi, ottimizzando l’uso delle risorse e riducendo gli sprechi. Attraverso l’analisi dei dati raccolti dai dispositivi connessi, le aziende possono prevedere malfunzionamenti e pianificare manutenzioni preventive, evitando costosi fermi macchina e prolungando la vita utile degli impianti. I singoli componenti sono interconnessi tra loro e comunicano con tutte le parti dell’azienda su più livelli (compresi MES e ERP) anche (e sempre più spesso) tramite cloud. L’afflusso costante di dati permette una gestione pervasiva di tutto l’impianto in tempo reale.
3. Lean Smart Factory
In una Lean Smart Factory, la fabbrica diventa un sistema interconnesso all’interno del quale i processi di ottimizzazione della produzione vanno a coinvolgere tutti i livelli. Per questo, nel passaggio al paradigma della Lean Smart Factory, l’introduzione di tecnologie abilitanti l’industria 4.0 comporta spesso la necessità di una riprogettazione dell’intero processo produttivo.
La Lean Smart Factory deve poi essere supportata da una serie di servizi che ne garantiscano il funzionamento continuo ed ottimale , è fondamentale che l’assistenza in campo da parte dei partner strategici, per il perfetto funzionamento dell’impianto, possa essere fornita con competenza anche da remoto, con efficienza e rapidità.
4. Interconnessione 4.0
L’ interconnessione 4.0 di macchine e impianti è il primo passo per accedere ai vantaggi della digitalizzazione del processo produttivo. L’Industria 4.0 ha portato all’introduzione di sistemi interconnessi che comunicano tra loro mediante l’Internet delle Cose (IoT). Queste tecnologie consentono una sincronizzazione perfetta tra macchine e sistemi informativi, ottimizzando l’uso delle risorse e riducendo gli sprechi. Attraverso l’analisi dei dati raccolti dai dispositivi connessi, le aziende possono prevedere malfunzionamenti e pianificare manutenzioni preventive, evitando costosi fermi macchina e prolungando la vita utile degli impianti.
Lo sviluppo tecnologico ha contribuito a rendere semplice un intervento che vent’anni fa poteva risultare complicato e oneroso.
5. Non esistono Macchine 4.0 ma Ambienti 4.0
Le macchine 4.0 non esistono. Esistono macchine, impianti e dispositivi che sono predisposti tecnologicamente e possiedono quanto necessario per poter essere introdotti in un ambiente 4.0; Il cuore del sistema non è più, pertanto, il “reparto produttivo” ma “l’ecosistema digitale esteso” dove il dato rappresenta il fattore differenziale di creazione del valore unitamente alla struttura informativa necessaria alla gestione di tale ecosistema. Per questo, anche in relazione agli incentivi confermati dal piano Transizione 4.0, la norma agevolante ha sin dall’inizio previsto che i beni oggetto di agevolazione debbano soddisfare alcuni requisiti (le “caratteristiche tecnologiche”) che non dipendono unicamente dal bene ma anche dal contesto informativo dell’azienda utilizzatrice potenziale beneficiaria. E proprio i requisiti di “interconnessione” e “integrazione” costituiscono l’elemento discriminante alla fruizione del beneficio
6. Tool di supporto remoto e assistenza rapida
Oggi siamo in grado di comunicare con tutte le principali tecnologie presenti negli stabilimenti produttivi. Non è necessario possedere impianti all’avanguardia per godere dell’efficienza di una smart factory.
In questo contesto la velocità di risposta può fare la differenza tra il successo e l’insuccesso, l’accesso a tool di supporto remoto e assistenza rapida è cruciale. Le aziende ora dotano i loro tecnici di strumenti che permettono di eseguire diagnosi e manutenzioni da remoto, riducendo drasticamente i tempi di inattività delle macchine. Questi strumenti consentono ai team di risolvere problemi senza la necessità di interventi fisici, offrendo un risparmio significativo sui costi e migliorando l’efficacia dei servizi post-vendita.
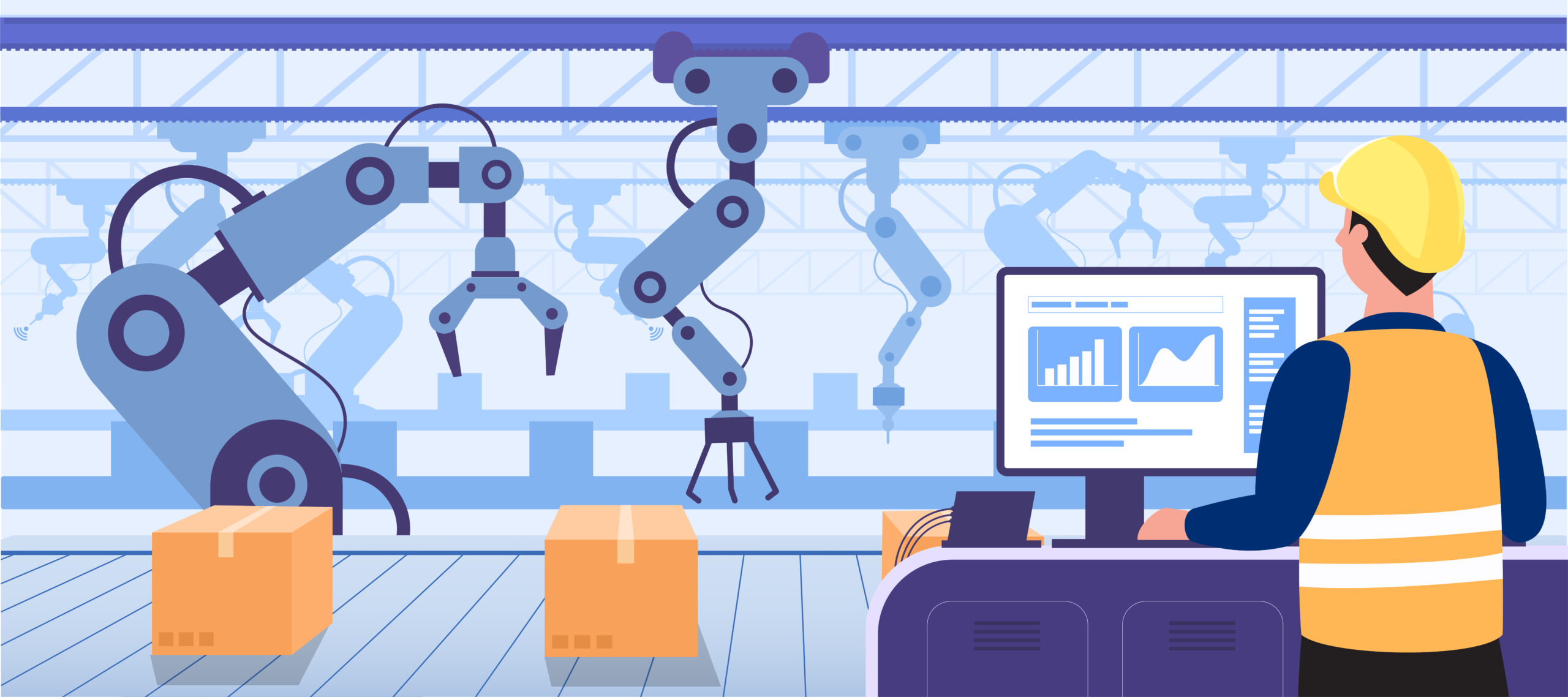
Conclusioni
In conclusione, l’automazione dei processi produttivi, i tool remoto, le interconnessioni tecnologiche 4.0 e le soluzioni personalizzate rappresentano pilastri fondamentali per le aziende che vogliono prosperare in un mercato sempre più tecnologico e competitivo. L’adozione di queste tecnologie avanzate non è più un’opzione, ma una necessità per chi cerca di ottimizzare le operazioni e garantire la massima qualità e efficienza nella produzione moderna.